Lotus
Esprit Manufacture
Photo's
taken of the Lotus Esprit production line at the Lotus Factory
at Hethel (pictures taken 1988).
Click on images
to enlarge
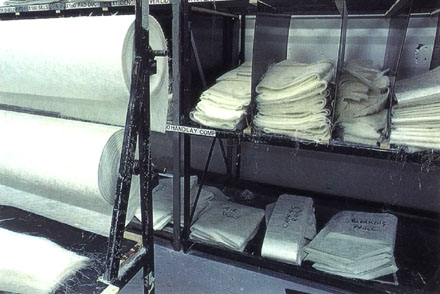
Rolls of glass
fibre mat is where it all begins. The mat is cut into shapes along
it's grain, using templates and stored ready for use.
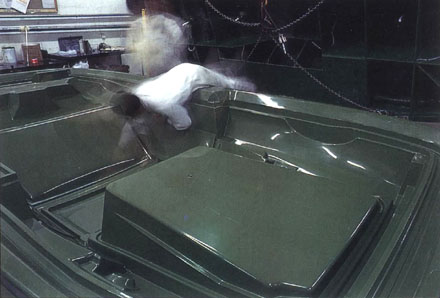
Here, the
female mold for an Esprit shell's top half is being polished with
a release agent, so that the gel coat will not stick when it is
released from the mold.
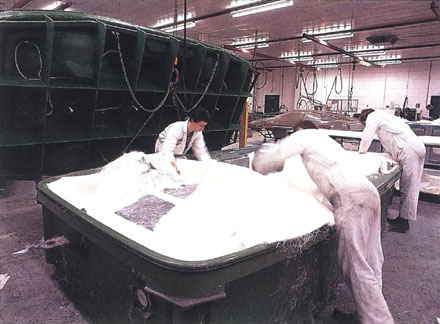
Then the pre-cut
glass fibre pieces are laid into the mold. Glass fibre rope, or
roving, is used to tie together sections which meet at awkward
angles.
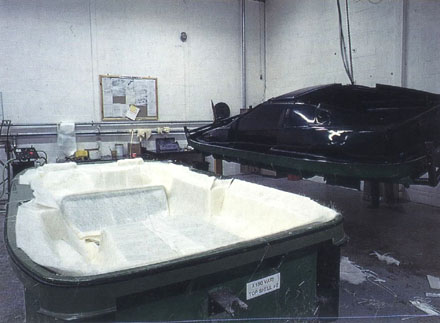
The male mold
is also sprayed with release agent and put into position. Resin
injection is the next step, the rubber seal, visible round the
mould's edge helps maintain the vacuum.
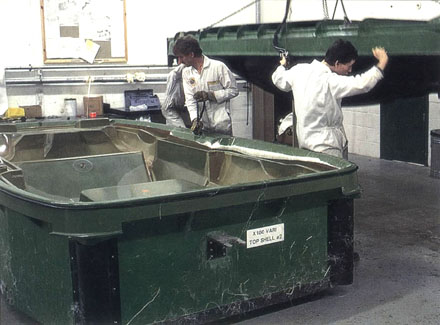
An hour after
it was injected, the resin has cured and the mould is popped with
compressed air to release it from the newly formed body. then
off comes the male moulds half, to reveal a brand new top body
section inside. It is still warm from the exothermic resin curing
process, but ready to come out.
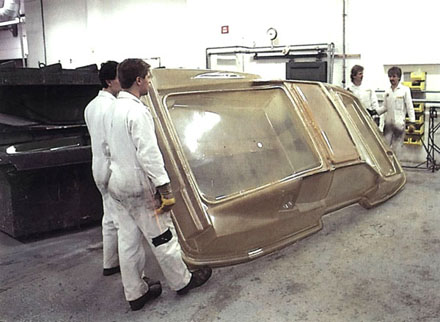
The shell
is removed from the mould, still warm. The shell is shiny on the
outside, but its glass fibre texture shows on the inside. Its
resin thinkness is closely controlled throughout, thanks to the
precesion of the VARI process.
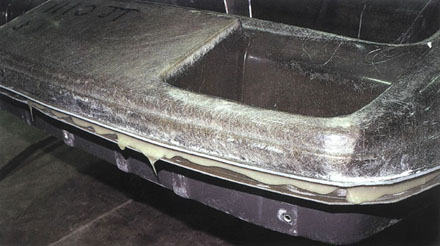
The top and
bottom halves are clapped and glued together, the excess epoxy
resin is squeezed out by the clamping pressure.
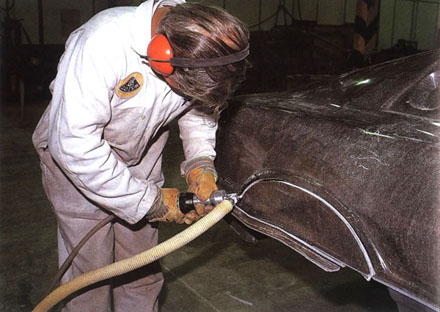
The translucent
body shell looks much less like an amorphous bob once the holes
and apertures are cut out. Amoung the first to be cut are the
wheel arches. The GRP is cut with an air-powered cutter.
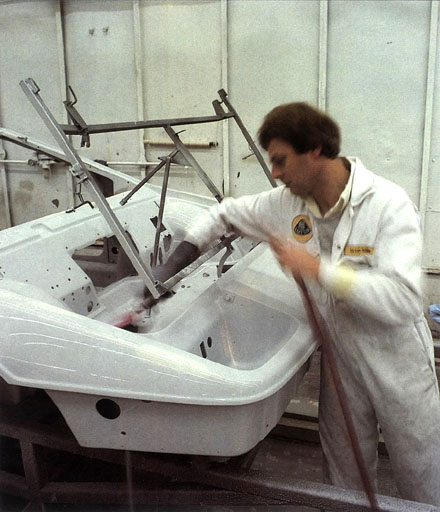
Between spraying
the many coats of paint, the body is rubbed down and washed to
ensure the smoothest finish possible.
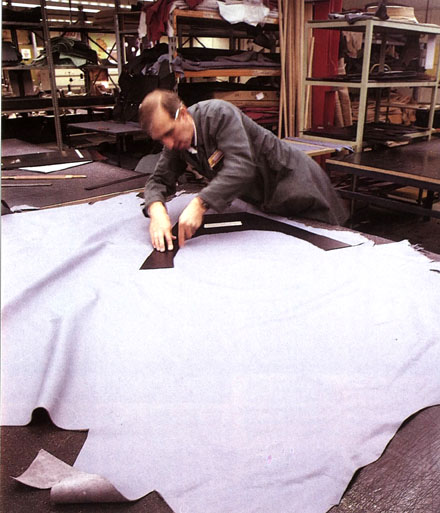
Mean while
the upholstery is being made for the interior. Here the leather
is being cut for the dash board binnacle.
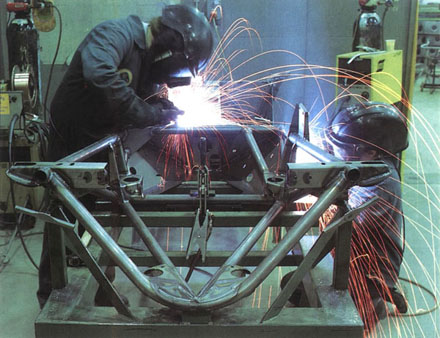
The chassis,
which is fabricated in sheet steel with a tubular engine cradle,
is welded together on a jig to ensure accuracy. Once complete,
it is sent away to be galvanised.
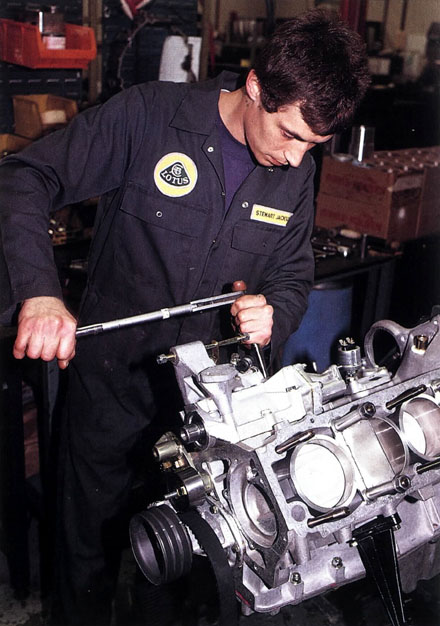
Here the engine
is assembled. Above work is being carried out to the oil pump.
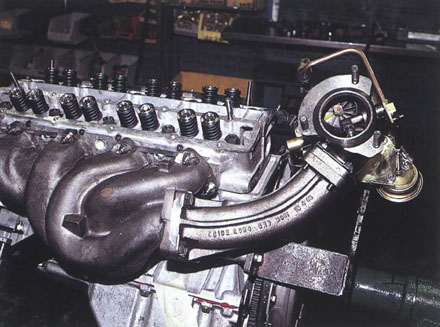
An Esprit
Turbo engine near completion.
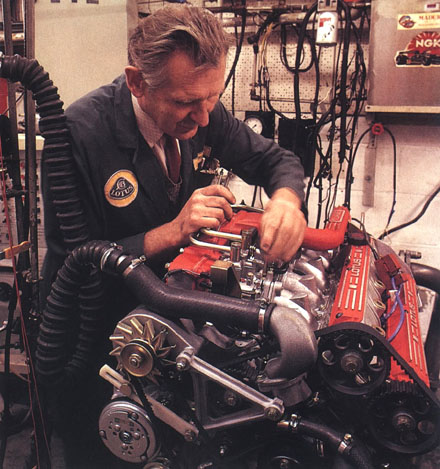
Newly built
engines are run the in test cell for half and hour, building up
speed in gentle stages. The the carburettor and ignition settings
are carefully adjusted and faults can be put right.
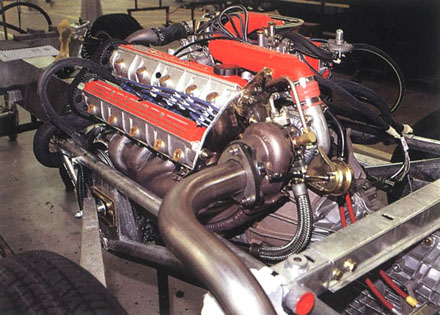
Finally the
finished engine is mounted to the chassis.
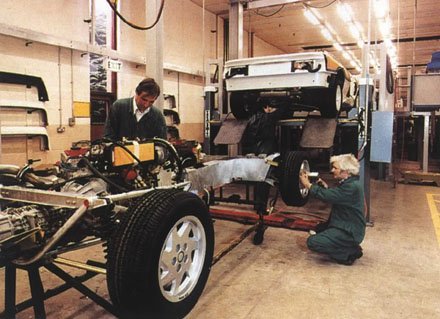
The finally
ancillaries are fitted the the chassis before the body shell is
fitted.
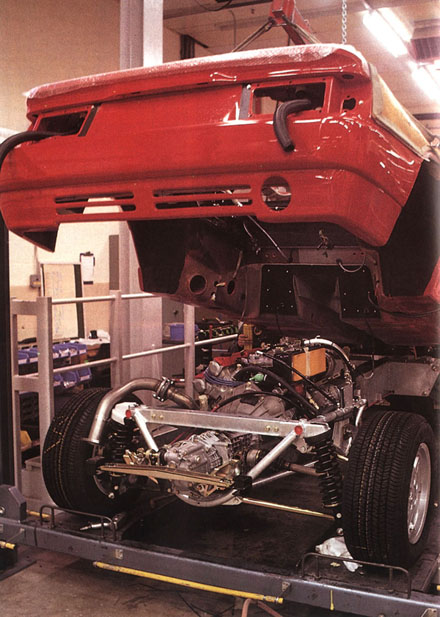
The body shell
is lowered to the chassis and fitted. The winch cables are hooked
into moulded protection plates to prevent body damage.
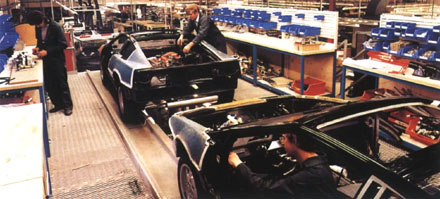
The asssembly
line; the interior seats, dashboard and doors are fitted.
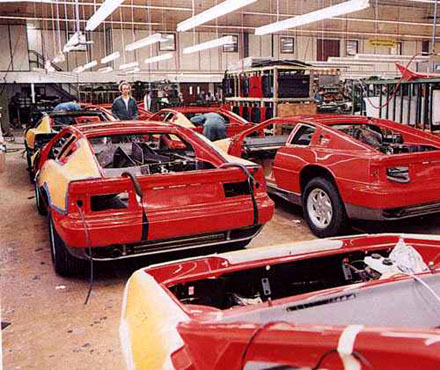

The final
part of the assmebly line.
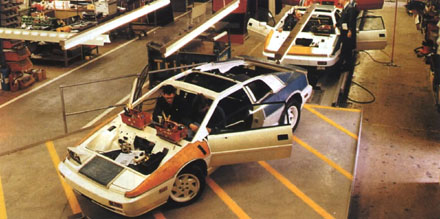
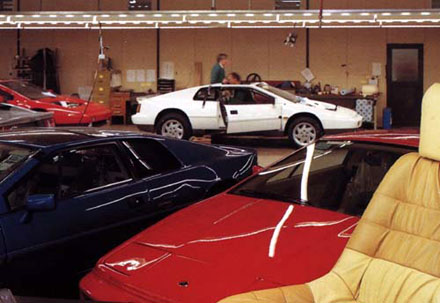
Finished Lotus
Esprit's park along side the final stage of the assembly line.
Click on images
to enlarge